
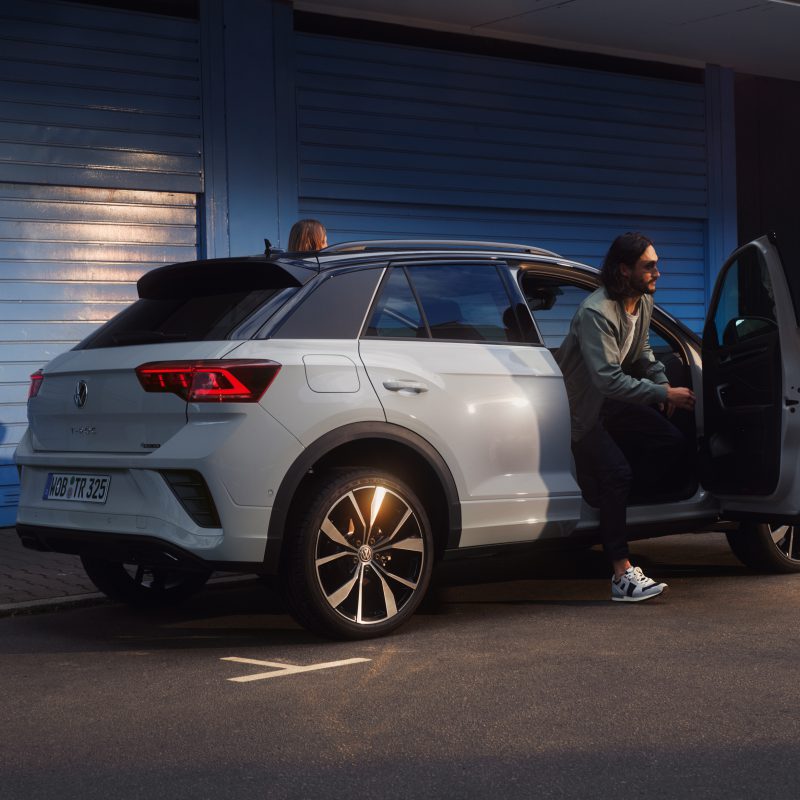
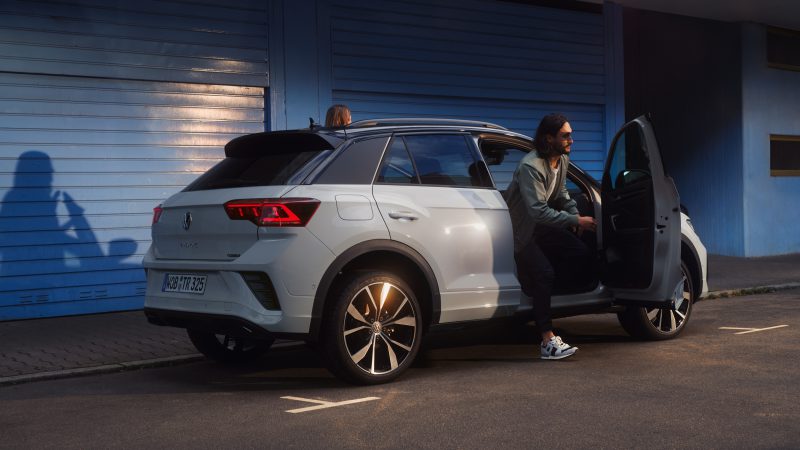
O novo T-Roc
Desde o início de janeiro, as linhas de Palmela produzem em exclusivo o novo T-Roc. Até chegarmos à produção em série há todo um trabalho de excelência e transdisciplinar que preparou mais um lançamento de sucesso de Palmela para o mundo.
Desde o início de janeiro, as linhas de Palmela produzem em exclusivo o novo T-Roc. Até chegarmos à produção em série há todo um trabalho de excelência e transdisciplinar que preparou mais um lançamento de sucesso de Palmela para o mundo.
-
O novo T-Roc
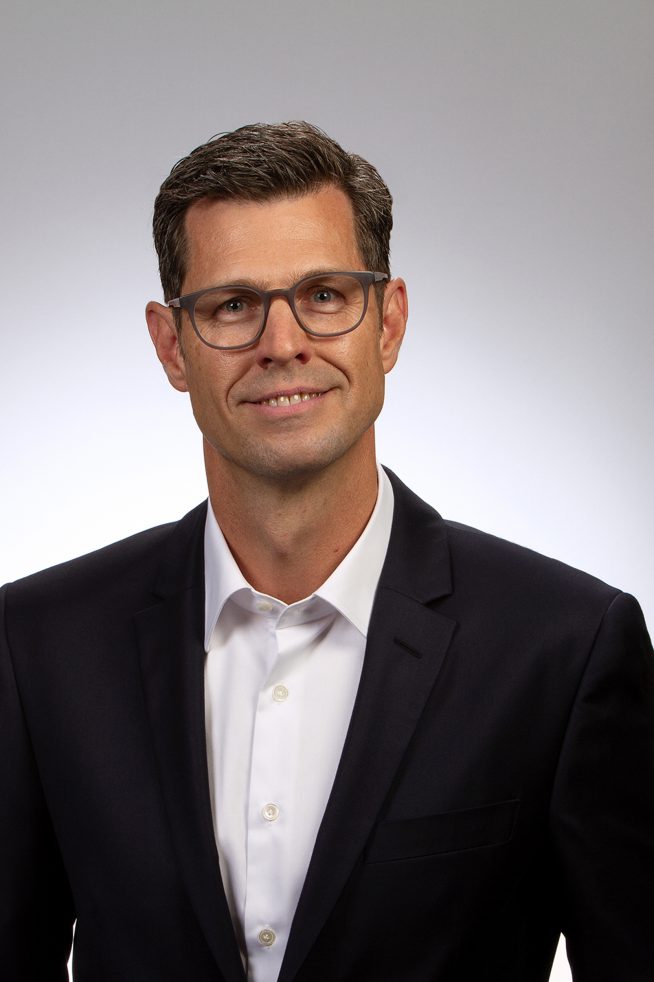
Thomas Hegel Gunther, diretor-geral
A receita perfeita para os bons resultados
Desde o seu lançamento em 2017, o T-Roc já vendeu mais de um milhão de unidades. Foi o segundo modelo da marca Volkswagen mais vendido na Alemanha, e em Portugal alcançou o feito histórico de ser, pela primeira vez, o modelo da marca Volkswagen mais vendido em Portugal. São razões para nos orgulharmos no nosso produto e deste primeiro ciclo da sua história.
Iniciamos o ano com o lançamento do novo T-Roc, um novo ciclo muito importante para nós.
O T-Roc chega ao mercado com novas propostas, que vão ao encontro dos desejos dos nossos clientes, aliando design, qualidade e uma experiência de condução ainda mais digital e conectada. É a receita perfeita para manter os bons resultados de vendas do seu antecessor e reforçar o nosso posicionamento como a «casa do T-Roc» nos próximos anos. O sucesso do produto não é só feito pelo cliente. Cria-se diariamente em cada uma das nossas equipas com a sua experiência e dedicação.
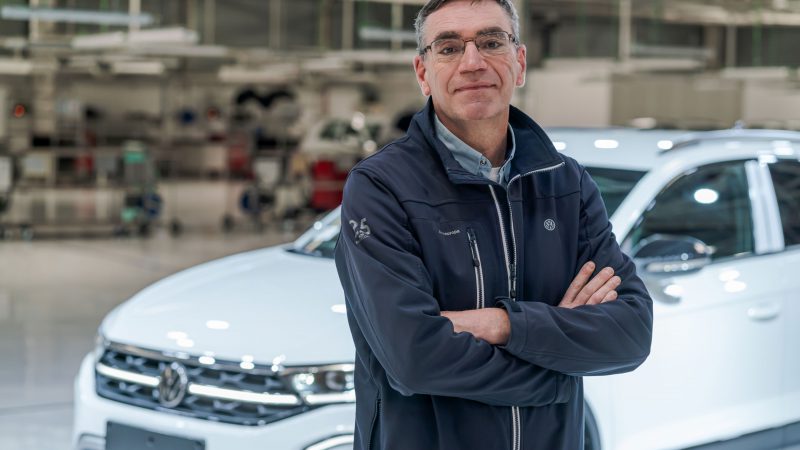
Rui Silva, especialista de alterações de produto, na área de gestão de produto e planeamento
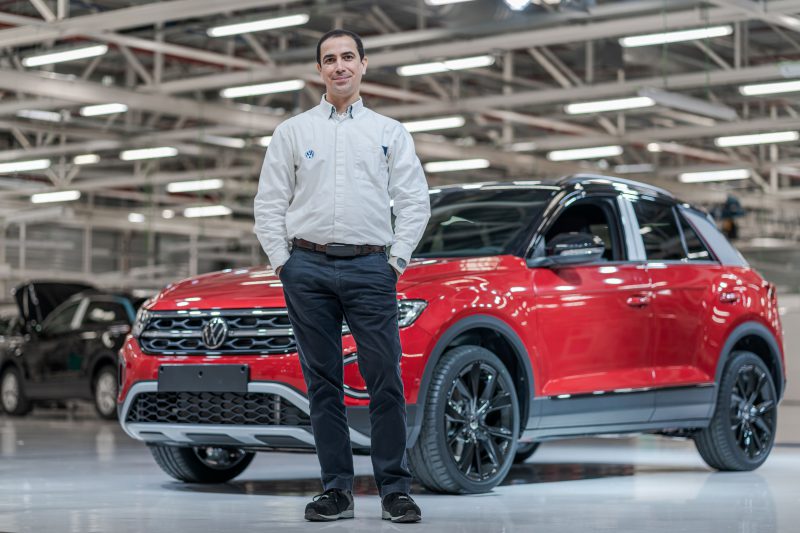
Mário Pedro, coordenador da oficina da pilot plant, na área de gestão de produto e planeamento
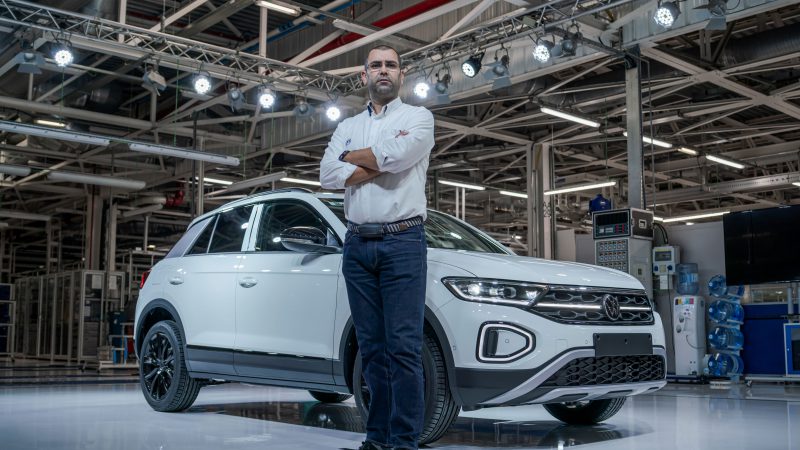
Marco Costa, coordenador de program readiness e disposition na logística
3 fases
VFF (Vorserien-Freigabe Fahrzeug) veículo para libertação da pré-série
PVS (Produktionsversuchsserie) veículo para testes de produção
Null-Series (0S) veículo da série zero para testar condições de série
No caso do novo T-Roc, os primeiros carros de VFF começaram a ser construídos na área de carroçarias em meados de janeiro de 2021 e os últimos carros de sério zero foram vendidos em CP8 na primeira quinzena de dezembro de 2021. No total foram construídos 229 carros.
Além destas três fases do projeto existe também o TPPA, que em português é o grémio de libertação de programas e projetos para série. É neste fórum que o projeto tem a aprovação para o início de produção. Entre o TPPA e o início de produção fazemos os chamados RPP ou «lebres», construção de carros de série duas semanas antes de início de produção.
Todos os carros são enviados para os nossos clientes internos na Alemanha, ou seja, a engenharia, a qualidade, o marketing e vendas.
Os carros são construídos na linha de produção e depois finalizados pela equipa da oficina da pilot plant e ECC, centro de competência eletrónica. Nas fases de VFF e PVS, a responsabilidade da construção é da pilot plant, mas na fase de série zero essa responsabilidade já passa para a produção, mantendo-se o apoio muito próximo da pilot plant.
A avaliação dos carros durante o processo de finalização é garantida pelos vários departamentos da qualidade (aceitação final, DKA , audit e centro de análises) e no final do processo os carros são sujeitos à aprovação dos nossos diretores antes da venda em CP8.
A capacidade de construção
A qualidade das peças compradas
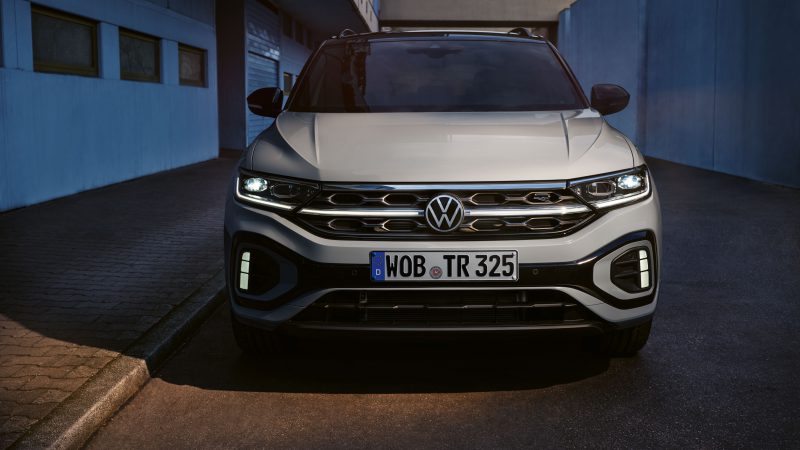
Da aprovação de qualidade de uma peça comprada até à produção em série
O trabalho começou cedo. «Em 2018 com a compilação das aprendizagens do lançamento do T-Roc anterior, em conjunto com a pilot plant informámos a engenharia de WOB de melhorias técnicas que gostaríamos de ver implementadas no novo T-Roc para melhorar o produto final como a qualidade e eficiência de montagem ao carro na nossa linha. Em finais de 2019 começámos a receber da engenharia de WOB as primeiras informações técnicas do produto e do departamento de compras, os potenciais fornecedores dos para-choques e seus componentes. Seguiu-se no início de 2020 a discussão e definição, com o departamento de planeamento de WOB, sobre as características críticas e significativas a controlar dimensionalmente.», explica Luiz Fonseca.
Paralelamente estabeleceram-se os primeiros contactos com o fornecedor principal SMP, fornecedores de componentes e fabricantes das várias ferramentas. No segundo semestre de 2020 iniciou-se o acompanhamento da fabricação das ferramentas em Portugal, Espanha, Itália e China. 2021 foi um ano atarefado com a chegada das várias peças e componentes para aprovação (controlo dimensional em máquina 3D CMM, ensaios de materiais em laboratório, testes de montagem em cubing e em veículos).
As peças sofreram correções e melhorias ao longo das fases de pré-series, por parte da engenharia e dos fabricantes das peças. Cada correção e/ou melhoria requereu mais uma série de testes e aprovação por parte do responsável em português? É o responsável da peça? (Bauteilverantwortliche) da qualidade peças compradas. Uma série de aprovação pode culminar numa nota 6 (a peça tem problemas graves e está rejeitada), nota 3 (a peça tem desvios às especificações, mas não prejudica o cliente e pode ser utilizada) ou nota 1 (a peça cumpre as especificações e pode ser montada). A produção em série só é autorizada quando se atinge pelo menos uma nota 3 para os para-choques completos e para cada um dos seus componentes.
Paralelamente à aprovação das peças, decorre a aprovação dos processos de fabrico dos para-choques e seus componentes de forma a garantir a qualidade e volumes requeridos, tarefa esta que também está a cargo do BTV.
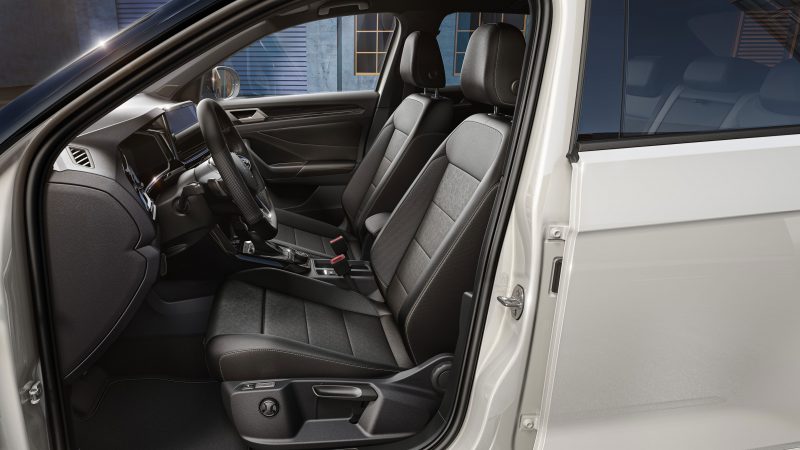
No interior
A grande mudança do T-Roc inclui a introdução de um cockpit completamente novo onde a grande diferença passa pelo seu exterior esponjoso e suave, o cluster passa a ser 100% digital e o display multimédia passa a ser destacado e de maiores dimensões.
O painel de instrumentos tem material novo, uma linha de costura característica que o atravessa em toda a sua largura e um painel central multifunções com um novo design. Estão agora disponíveis novas cores em todas as peças decorativas do interior, linhas de costura decorativas nos painéis interiores das portas da frente, a inclusão de assentos elétricos e novos tecidos e padrões.
Paulo Godinho, acredita que «para o cliente final, o novo material no painel de instrumentos garante uma maior sensação de qualidade e conforto ao toque e à vista. As linhas de costura características, tanto no painel de instrumentos como nos painéis interiores das portas, introduzem estilo e requinte, elevando a qualidade do interior do T-Roc.»
O novo painel central multifunções «touch screen», com a opção de 8 ou 9.2 polegadas, destaca-se pelo seu design arrojado e permite uma melhor interação do condutor com o carro.
Os assentos elétricos trouxeram conforto e tecnologia e o cliente tem agora a possibilidade de escolher esta opção.
Mais digital e conectado
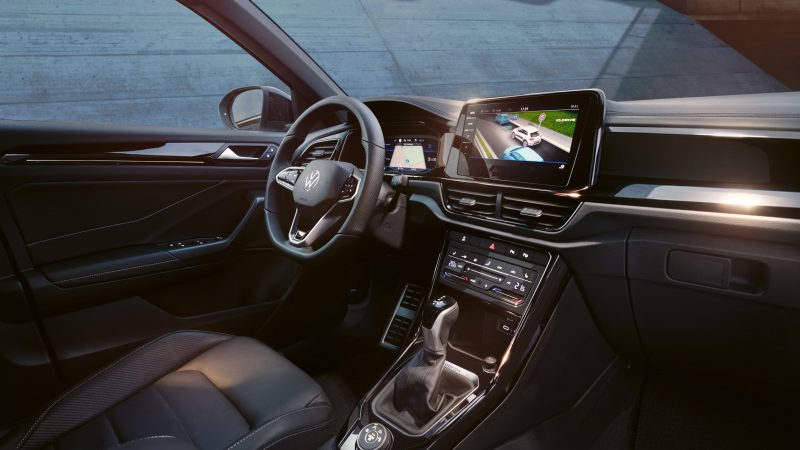
Infotainment
As grandes alterações concentram-se na melhoria da acessibilidade e facilidade de compreensão das várias funções por parte do cliente, estando estas claramente mais percetíveis e simples de usar.
Novas tecnologias
- faróis «inteligentes» IQ.LIGHT LED Matrix
- Abertura e fecho do portão «Easy Open & Close». Permite ao utilizador carregar e descarregar o compartimento de forma mais cómoda, não necessitando utilizar as mãos, bastando-lhe simplesmente uma passagem com o pé por baixo do para-choques traseiro, para que o mesmo se abra e feche.
- Muito útil no regresso de uma ida ao supermercado com sacos de compras nas mãos.
- Sistema de assistência à condução IQ.DRIVE Travel Assist. Este último combina em si mesmo vários assistentes (Lane Assist, Adaptative Cruise Control, Front Assist, Sign Assist, Traffic Jam Assist, Proactive Occupant Protection System e GPS) e permite uma condução parcialmente autónoma até um limite de 210 km/hora. Estes sistemas de assistência à condução conjugados, permitem que o novo T-Roc se enquadre no nível 2 de condução autónoma (escala de 0 a 5, em que 5 significa autonomia total).
Apesar do sistema permitir que o T-Roc se desloque de forma autónoma dentro da faixa de rodagem, tendo em conta a velocidade permitida pelos sinais de trânsito e pelo tráfego na estrada com o sistema Stop&Go, a responsabilidade de uma monitorização contínua da condução cabe sempre ao condutor!
Stop&Go
O novo T-Roc ficou ainda mais seguro com a melhoria dos sistemas já existentes como o Side Assist, Parking Assist, Predictive Adaptative Cruise Control ACC, Lane Assist, Proactive Occupant Protection System.
Outra novidade foi a substituição de vários botões físicos por tecnologia touch (de contacto), como por exemplo o controlo automático do ar condicionado. Foi também introduzido o HOD (Hands-On Detection), que permite detetar e avisar o condutor quando, por distração ou outro motivo, retira completamente as mãos do volante em situações de condução semiautónoma.
Em última instância, se os sistemas (p.e. o HOD) detetarem ausência da monitorização por parte do condutor, o carro autonomamente abranda até parar por completo, assinalando esta manobra de emergência ligando os «4 piscas».
O maior desafio? Foi o trabalho de correção de falhas de produto e do processo eletrónico. Com o novo T-Roc temos aproximadamente 40% de alterações eletrónicas que passaram obrigatoriamente por alterações ao nível da programação dos testes elétricos, conseguimos ainda assim estar atualmente com índices de qualidade eletrónica em fim de linha (EOL - End of Line - CP6), comparáveis aos índices do final de 2021.
Pedro Silva
Descobre mais sobre a nova tecnologia do T-Roc
IQ.LIGHT LED Matrix Faróis LED com ajuste automático da intensidade de luz, para não encadear carros que se desloquem na mesma faixa ou em sentido contrário.
Lane Assist Sistema que permite a leitura das linhas da faixa de rodagem, avisando o condutor no caso de ultrapassagem acidental das mesmas
Adaptative cruise Control ACC – Sistema automático que permite um controlo da velocidade recorrendo à leitura em tempo real do tráfego na estrada, garantindo a distância pré-definida para com o carro da frente.
Front Assist A câmara/sensor frontal avalia a distância do carro que se desloca à sua frente, avisando o condutor em caso de perigo iminente de colisão e inclusive, numa situação extrema, efetuando automaticamente a necessária travagem de emergência, para evitar o acidente. Este sistema é também usado dentro das cidades quando um «peão» acidentalmente se coloca à frente do carro.
Sign Assist Sistema suportado por uma câmara frontal, que lê e interpreta os sinais de limite de velocidade dando a informação, tanto ao condutor como a todos os sistemas do carro que desta informação necessitem para a execução das suas funções.
Traffic Jam Assist Sistema que permite uma condução parcialmente autónoma, até aos 59 km/h, sempre de acordo com as condições do tráfego na estrada, durante uma situação de para/arranca - Stop&Go (disponível apenas para carros com a opção de caixa automática).
Proactive occupant protection system Sistema que monitoriza um potencial acidente ou condução descontrolada, altivando o aperto dos cintos de segurança do condutor e do passageiro, fechando os vidros das portas e teto de abrir, por forma a minimizar as possíveis consequências para os ocupantes do veículo.
A gestão de fornecedores
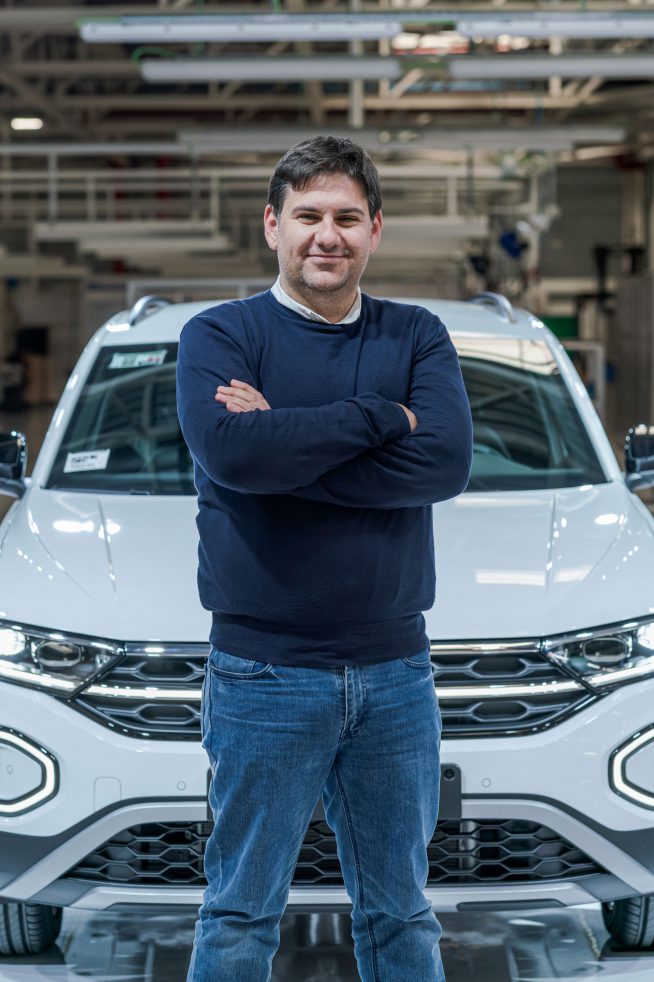
Mário Carromeu, especialista de gestão de peças compradas (KTM), responsável pelo apoio a fornecedores e gestão de crise, área de compras e aprovisionamento.
Mário Carromeu explica-nos o trabalho da equipa de gestão de fornecedores, da área de compras e aprovisionamento. Em teoria, o seu trabalho começa com as nomeações dos fornecedores para o novo projeto, aproximadamente dois anos antes do início de produção. Para o novo T-Roc, o trabalho começou em 2018 com o acompanhamento dos sourcings para este projeto, assegurando os conceitos logísticos e de produção da fábrica e a colaboração com o departamento de compras central para a nomeação de fornecedores locais.
«Foram definidas as peças críticas do projeto e a garantia da disponibilidade dos itens críticos para a pré-série. Foram feitos os comissionamentos com os fornecedores nomeados para o cumprimento dos prazos das diferentes fases do projeto, assegurando a disponibilidade de peças até ao início de produção e a capacidade instalada dos mesmos. Validámos os conceitos para as ferramentas com os fornecedores e a sua exequibilidade técnica.
Controlámos o tempo de execução e a qualidade das ferramentas e equipamentos de acordo com os prazos de projeto. Trabalhámos com a qualidade para a qualificação de peças e processos, incluindo os testes de capacidade, em dois dias de produção. Da nossa agenda também fez parte a resolução de problemas diversos com os fornecedores desde a gestão da pandemia, à validação de novos processos ou alterações de peças ao longo do projeto.», refere Mário Carromeu.
Novos fornecedores
Vários e destacam-se três dos mais importantes: as decorações interiores pintadas da Fehst de Braga, os faróis da Valeo em Tânger, Marrocos e os refletores da Varroc, na Turquia.
Novas ferramentas
Como não há alteração na carroçaria do carro, mantêm-se as anteriores ferramentas de estampagem. Porém, foram introduzidas cerca de 185 novas ferramentas de injeção.
Excelência e superação na curva de lançamento
«O grande desafio foi manter as datas de entrega dos carros aos clientes internos. Estes carros são utilizados para processos de homologação e para testes obrigatórios da qualidade, sem os quais não podíamos avançar para a produção em série. As diversas paragens foram contornadas com planos de contingência, antecipando e aumentando a produção diária dos carros de pré-série na montagem. A logística conseguiu garantir as peças do projeto em tempo útil, antecipando a sua entrega. Além disso, as peças críticas de produção foram reservadas para os carros de pré-série. A oficina da pilot plant e os departamentos de qualidade envolvidos asseguraram o processamento dos carros durante os períodos de paragem de forma a garantir o sucesso do plano. Graças às atividades desenvolvidas pela equipa, todos os carros foram entregues de acordo com as datas estabelecidas com os clientes. É um verdadeiro exemplo de trabalho em equipa para um bem maior.»
«Comparando com as valorizações de produto anteriormente realizadas, esta correu francamente melhor.
Houve um conjunto de lições aprendidas nos lançamentos anteriores que foram materializadas agora, p.e. a verificação virtual das cablagens e dos conteúdos dos carros de pré-série, criação de carros virtuais para verificação dos conteúdos para os “mercados exóticos” (p.e.: Egipto, Marrocos, Coreia do Sul, entre outros). Tudo isto, aliado à experiência acumulada pela equipa, culminou neste excelente resultado.»
Mário Pedro, Rui Silva e Marco Costa
«Todo o processo de lançamento foi muito desafiante. Por um lado, em apenas duas semanas fizemos a transição dos processos do antigo para o novo T-Roc usando as mesmas instalações. Por outro lado, a curva de lançamento de produção foi muito “agressiva”. Acredito que não tivemos até hoje outro modelo na Volkswagen, que desde o dia 1 de produção até alcançar a sua produção máxima, o tivesse feito em tão pouco tempo. Em termos de qualidade, o nosso desafio foi manter o nível de qualidade em audit (cliente final), para que a fábrica não sentisse oscilações neste indicador. Foi um desafio enorme, mas a dedicação de todos os envolvidos fez com que fosse superado.»
Paulo Godinho
Carlos Rodrigues
«A equipa fez um excelente trabalho. Alcançámos plenamente a expetativa de um lançamento de sucesso em dois aspetos essenciais. Garantimos o início de produção, ao nível de construção, sem pontos em trabalho com a engenharia e na qualidade do produto final, alcançámos um índice de qualidade em linha com a classe de qualidade do seu antecessor.»
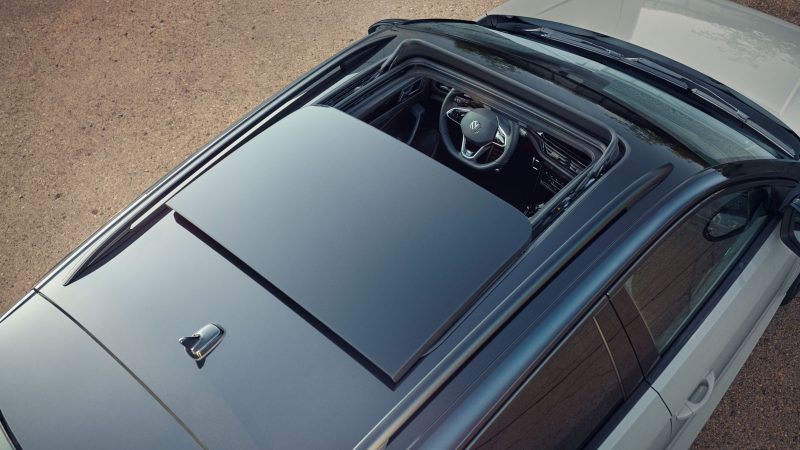
Formação em linha
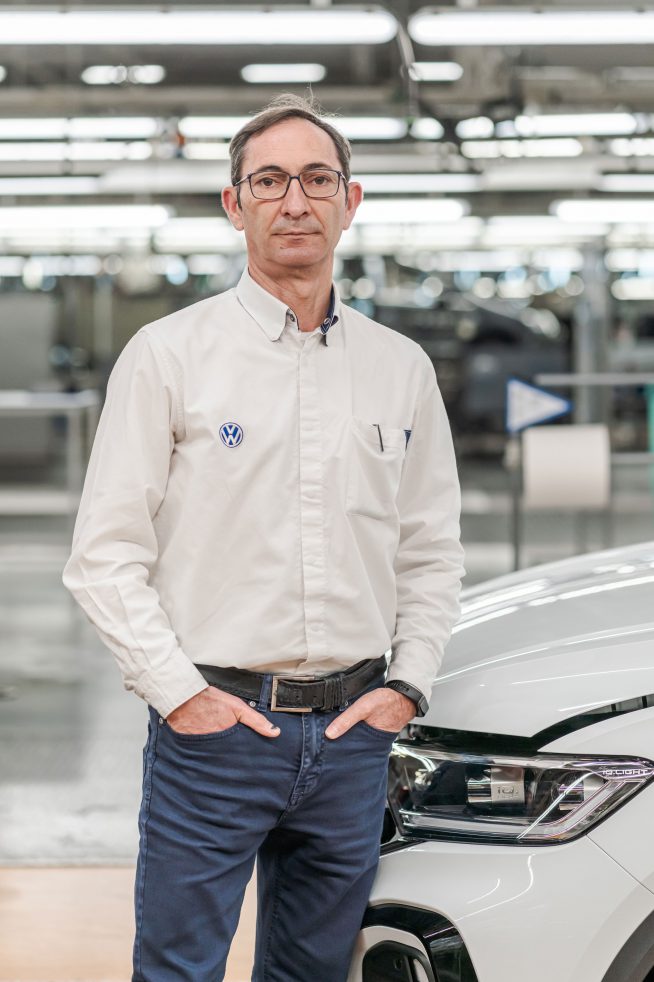
«Entre projetos novos e facelifts este é meu sexto na equipa da montagem. É muito gratificante e dá-me uma enorme satisfação. Foi um facelift com várias alterações de peças e, como é natural, há sempre coisas a melhorar ao longo das várias fases de construção. Ao longo destes anos todos nós que participámos em lançamentos fomos ganhando experiência e conhecimento. Agora encaramos tudo isto com naturalidade e o resultado final é “fabuloso”».
José Ferreira, supervisor de produção da montagem
José Ferreira liderou a equipa da montagem na construção dos carros em linha com a missão de envolver todos os colaboradores das várias zonas logo no início da construção. A sua missão era garantir que existiam todas as condições de processo, ergonomia, ferramentas ou logística para que o início a produção fosse o mais tranquilo possível.
A equipa de produção passou por um processo de formação para o novo produto. Ferreira refere que «todos têm bastante experiência e conhecimento pelas funções que desempenham. Neste caso, tratando-se de um facelift, a formação focou os processos e peças novas. Para as zonas de linha foram criadas algumas formações específicas, como por exemplo, a montagem dos novos faróis. Os conteúdos da formação incluíram módulos relacionados com o cockpit, para-choques frontal e traseiro, faróis, painéis de portas, farolins traseiros, volante, manete de velocidades e também a nível de digitalização.»
A maior parte da formação foi feita em linha durante a construção dos carros com as novas peças, abrangendo as quatro equipas. Apenas nos casos em que o processo de montagem alterou a formação foi dada fora de linha num carro de treino. «Por exemplo, nas formações mais específicas como a dos faróis, a Zona E deu treino a cerca de quarenta operadores divididos pelos quatro turnos.», explica Ferreira.
Um produto novo, uma pandemia, novas formas de trabalho
«A pandemia não nos permitiu viajar para acompanhar presencialmente os processos de fabrico dos nossos fornecedores, ou simplesmente recebê-los na fábrica para reunir e encontrar soluções para resolver os problemas de qualidade que tínhamos em mãos. Esta nova realidade veio impulsionar novas oportunidades de desenvolvimento das tecnologias de informação nos nossos processos de trabalho. As reuniões digitais passaram a ser rotina, o teletrabalho foi introduzido e hoje já colocamos sempre como primeira opção a videoconferência, antes de planear qualquer deslocação ao exterior da fábrica.»
Paulo Godinho
«Foi um projeto como nunca antes visto. Foi o primeiro projeto onde a responsabilidade foi dada a 100% ao nosso departamento local. Desde a gestão do projeto dos tempos das peças criticas, ao controlo da execução de todas as ferramentas e equipamentos para as peças criticas definidas.
O departamento central de gestão de fornecedores confiou no nosso trabalho e nomeou o seguimento do projeto na nossa equipa, dando continuidade e valorizando o bom trabalho já antes efetuado no T-Roc 2017.
Fomos chamados pela gestão de projeto e compras de produção a participar em todos os aspetos do projeto, na própria gestão da pandemia e igualmente fomos requisitados a ajudar e gerir os itens críticos do T-Roc Cabrio, em Osnabrück.
O seguimento do projeto foi por videochamada, uma situação completamente nova e desafiante. Nos projetos anteriores era dada prioridade ao seguimento local. A adaptação foi difícil em tão curto espaço de tempo, mas conseguimos recorrer a toda a rede de gestão de fornecedores em todos os gabinetes regionais. Tivemos o apoio dos colegas na China a seguir as ferramentas que estavam em construção no país e a ultrapassar os constrangimentos logísticos no seu envio para a Europa.
Passamos por dois confinamentos em Portugal, com o risco enorme de atrasos e paragens dos fabricantes de moldes e fornecedores devido à pandemia, que acabou por acontecer em alguns períodos. Também tivemos de gerir a situação de confinamento noutros países porque os ferramenteiros e os próprios fornecedores estão espalhados por todo o mundo. Conseguimos com um enorme esforço recuperar dessas paragens e cumprir os prazos do projeto.
A nossa equipa foi das primeiras a voltar ao trabalho, depois dos confinamentos, a viajar em situações adversas, por vontade da própria equipa, não só em Portugal como em outros países para verificar ferramentas e gerir situações criticas, tentado gerir igualmente o risco provocado pela situação em termos profissionais e pessoais.»
Mário Carromeu