Segurança industrial
Montagem vence 3.ª edição de Prémio de Segurança Industrial
Prémio de Segurança Industrial relativo ao ano de 2023 é entregue à área da Montagem na primeira reunião de 2024 com a Comissão de Segurança e Saúde no Trabalho.
-
Montagem vence 3.ª edição de Prémio de Segurança Industrial
Foi no dia 6 de fevereiro, que se procedeu à cerimónia de entrega do 3.º Prémio de Segurança Industrial, relativo às práticas de 2023. Neste ano que passou e pelo segundo ano consecutivo, a área que se distinguiu na prevenção de acidentes foi a Montagem.
O Prémio de Segurança Industrial, promovido pelo departamento de segurança industrial da área de RH&O, tem como propósito motivar os colaboradores e a liderança e também fortalecer o seu envolvimento para a melhoria das práticas de segurança nas áreas de produção. Este gesto teve lugar na primeira reunião de 2024 da Comissão de Segurança e Saúde no Trabalho, onde estiveram presentes membros das várias áreas e a gestão de topo.
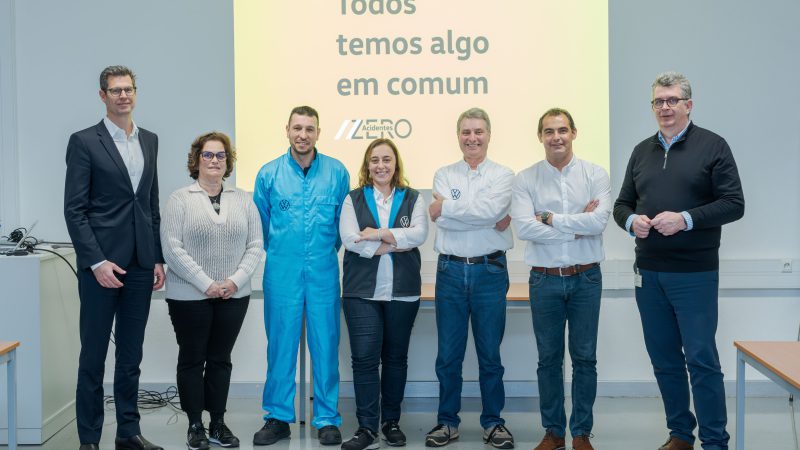
Thomas Hegel Gunther (diretor-geral), Paula Colaço, Nelson Ferreira, Ana Rebelo e Vítor Marques (equipa SI), José Prior (chefe dept. serviços, SI e conceitos estratégicos) e Dieter Neuhäusser (diretor RH&O)
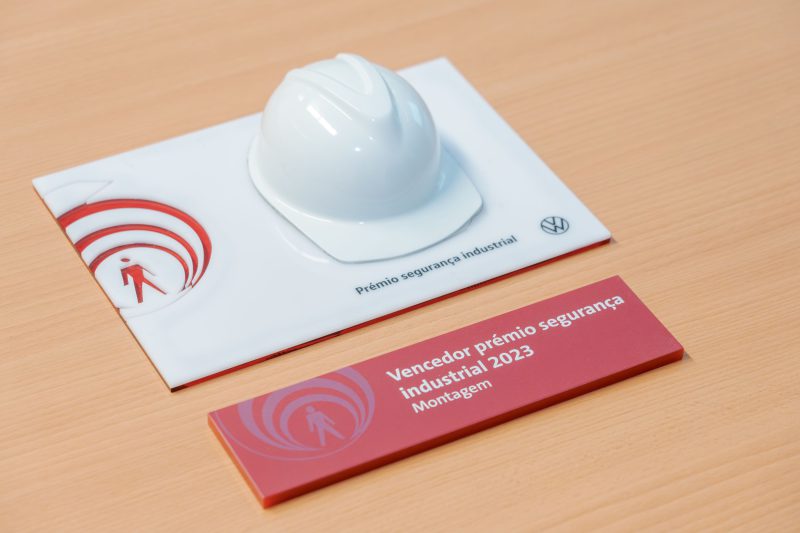
Exemplo disso foi a retirada de pinos dos transportadores das portas, uma pequena peça que antes servia para apoiar as portas do MPV. Esses objetos, agora desnecessários, criavam uma zona de possível impacto, onde os colaboradores podiam bater com o braço ou eventualmente com a cabeça. Por esse motivo procedeu-se à sua retirada na totalidade dos transportadores, contribuindo para a desobstrução e melhoria da segurança no local de trabalho. De notar que, sendo esta uma linha extensa, embora os pinos sejam de pequeno porte, este trabalho de remoção implicou bastante empenho da equipa de manutenção da montagem que promoveu a remoção de mais de 190 pinos.
Nessa mesma área foi ainda identificada uma segunda situação de potencial insegurança. Por vezes, nos transportadores das portas, ficavam esquecidas caixas dos puxadores que, embora leves, poderiam cair e causar um acidente ou incidente. Por esse motivo, procedeu-se à reprogramação de um sensor já existente de forma a que se, a partir deste momento, alguma caixa ficar esquecida, a linha para até que a mesma seja removida do transportador.
António Pires, team leader da zona B2 da montagem, dedicou-se afincadamente à renovação da plataforma onde os colaboradores que lidera exercem funções. Esta plataforma encontrava-se com o piso desgastado e com desníveis, o que significava um risco de queda e/ou escorregamento. A remodelação da estrutura e do piso foi concluída, ultrapassando os níveis de segurança inicialmente oferecidos pela antiga plataforma, acrescentando à remodelação a pintura antiderrapante que não existia anteriormente, no local onde os colaboradores teriam mais risco de escorregar.
António Pires acrescenta que esta alteração foi um fator de motivação tanto para os colaboradores como para si que, enquanto líder, considera a segurança dos seus colaboradores, um fator extremamente importante.
Todas estas situações foram também acompanhadas por Paulo Machado, chefe de departamento da montagem.
Assiste ao vídeo
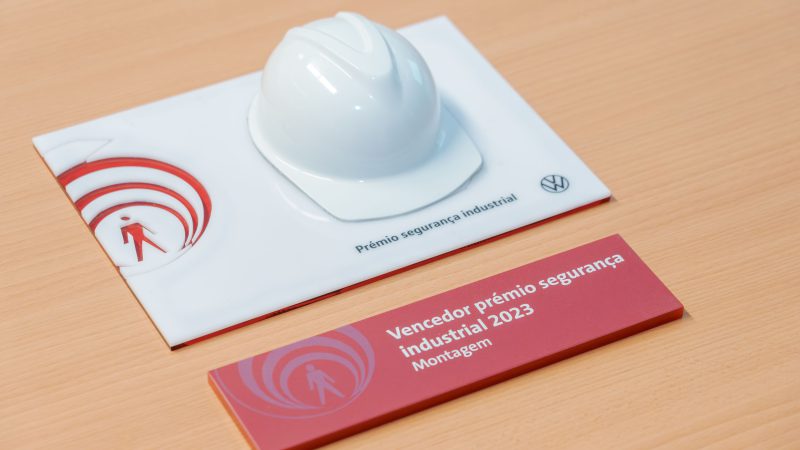
O troféu
O troféu de segurança industrial tem um cunho da casa. Com desenho de Alexandre Pires, especialista de Corporate Design e Brand Keeper, no departamento de comunicação e relações governamentais e de Avelino Patinha, Die Designer, da UNCC. Esta foi provavelmente a mais pequena peça feita na UNCC.
Após testes de conceito foram desenhados todos os elementos em 3D e 2D, verificando se funcionavam todos juntos e se passava a mensagem proposta. Depois de todos os elementos montados através de peças modeladas em 3D foi confirmado…tínhamos um troféu!
Após esta etapa, os dados em 3D do capacete foram passados à UNCC para que pudesse desenvolver e fresar a peça e os dados em 2D para um fornecedor externo produzir a base de acrílico.
Antes de chegar à fresadora foi necessário uma análise cuidada da geometria pela equipa de Die Design e otimização de alguns pontos, de modo a termos um “Design for Manufacturing”. Após essa análise, a geometria é entregue à equipa de CAM, que é responsável por criar toda a linguagem de máquina para que o bloco maciço seja maquinado e no final apresente a geometria pretendida. Estando todo o código/ linguagem de máquina desenvolvido, podemos iniciar a maquinação do bloco de alumínio numa das nossas fresadoras pequenas e percorrendo todas as linhas até obter a geometria final.
O empenho de todos à volta de uma peça que todos possam dizer que também fizeram parte foi impressionante: Mário Santos, Rodrigo Leal, Rui Oliveira, Avelino Patinha, Francisco Simões, Flávio Neves e Tiago Pereira (UNCC) e João Soeiro (Pintura).
A cor final é o Pure White do nosso T-Roc e a pintura foi também da casa.
O empenho de todos à volta de uma peça que todos possam dizer que também fizeram parte foi impressionante: Mário Santos, Rodrigo Leal, Rui Oliveira, Avelino Patinha, Francisco Simões, Flávio Neves e Tiago Pereira (UNCC) e João Soeiro (Pintura).
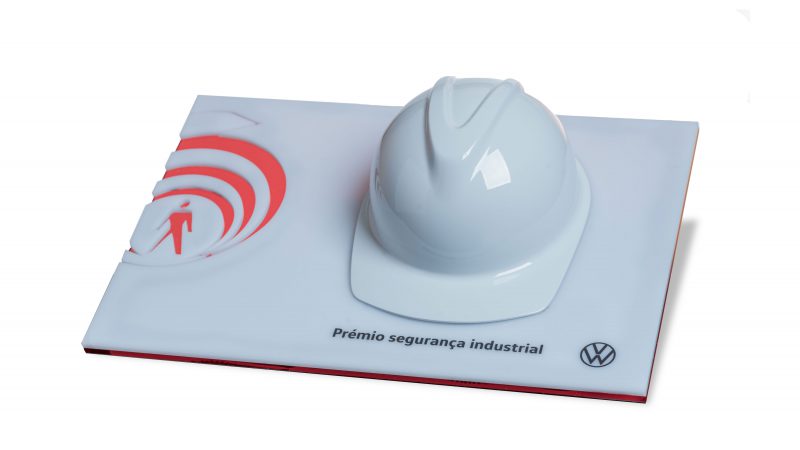